Requirement in Basic Ground
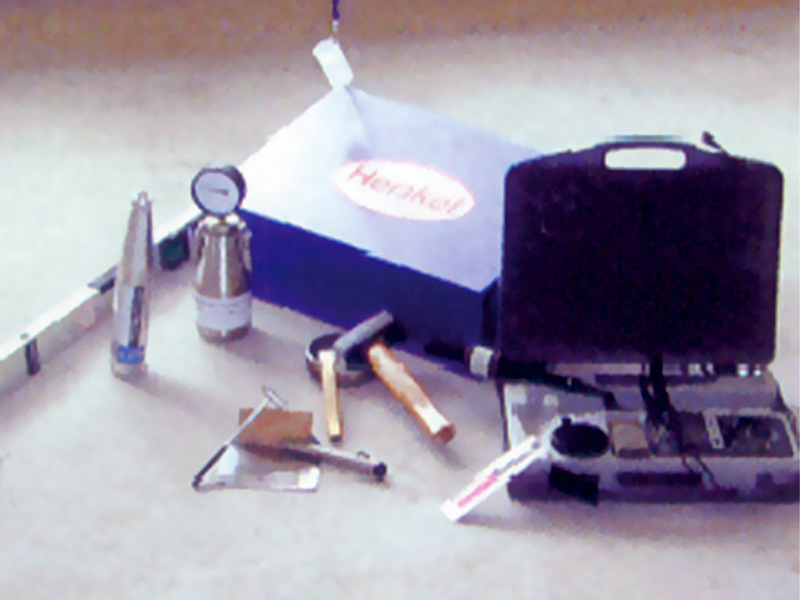
Ground and Environment Detection
- The concrete floor must be leveled with mortar 15-20 days in advance before paving the floor of Borford. The leveling height is 5mm lower than the design height of the ground. The leveling surface is smooth.
- Use temperature and humidity meter to detect temperature and humidity. The indoor temperature and surface temperature should be 15-30 ° C. Construction shall not be carried out below 8C and above 30 ° C. The relative humidity directly to the construction shall be between 20% and 75%.
- The moisture content of the base course shall be tested with a moisture tester, and the moisture content of the base course shall be less than 5%. The strength of the base course shall not be lower than the requirements of C-20. Otherwise, proper self-leveling cement shall be used to strengthen the strength of the base.
- Use a hardness tester to test the surface hardness of the base course. The surface hardness shall not be less than 1.2 MPa.
- Use the flatness tester to check the flatness of the floor surface. The unevenness of the floor surface within any 2 square meters shall be less than 2 mm. Otherwise, proper self-leveling cement shall be used for leveling.
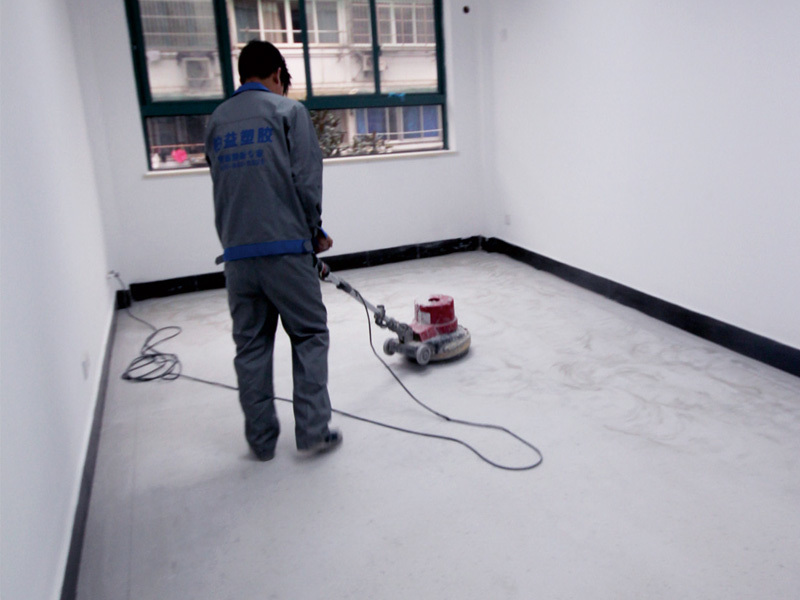
Ground Pretreatment
- The floor grinder with a total of 1500 watts or more shall be equipped with appropriate grinding discs to polish the floor, remove paint, glue and other residues, polish the convex and loose areas, and remove the hollowed plots.
- The national industrial vacuum cleaner is used to clean the ground.
- For the cracks on the floor, stainless steel reinforcement, polyurethane waterproof adhesive and quartz sand can be used to repair.
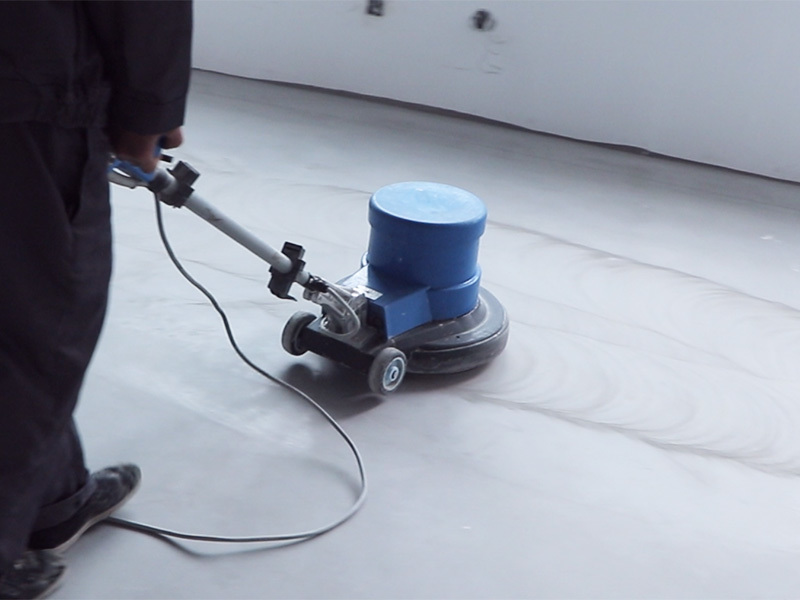
Render
- The leveling layer of absorbent base concrete and cement mortar shall be sealed with multi-purpose interface treatment agent according to the use regulations.
- For dense base course, such as ceramic tile, water, grindstone, marble, etc., it is recommended to use dense interface treatment agent for priming treatment.
- If the moisture content of the base course is too high (>5%), but it needs to be constructed immediately, epoxy interface treatment agent (or waterproof self-leveling) can be used for priming treatment.
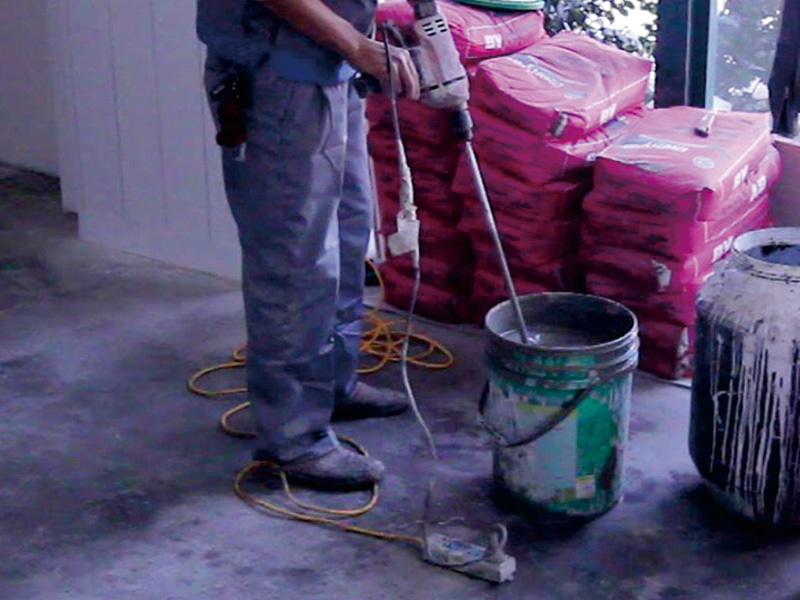
Stirring and Mixing
-
A bag of self-leveling shall be poured into a mixing bucket containing clear water according to the water and ash ratio specified in the use, and mixed while pouring.
In order to ensure uniform self-leveling mixing, a high-power low-speed electric drill with a special mixer must be used for mixing.
-
After self-leveling and stirring to uniform slurry without caking, let it stand and ripen for about 3 minutes, and then briefly stir again.
-
The proportion of water and ash shall be strictly controlled. Too much water will reduce the strength after curing, while too little water will affect the fluidity of self-leveling.
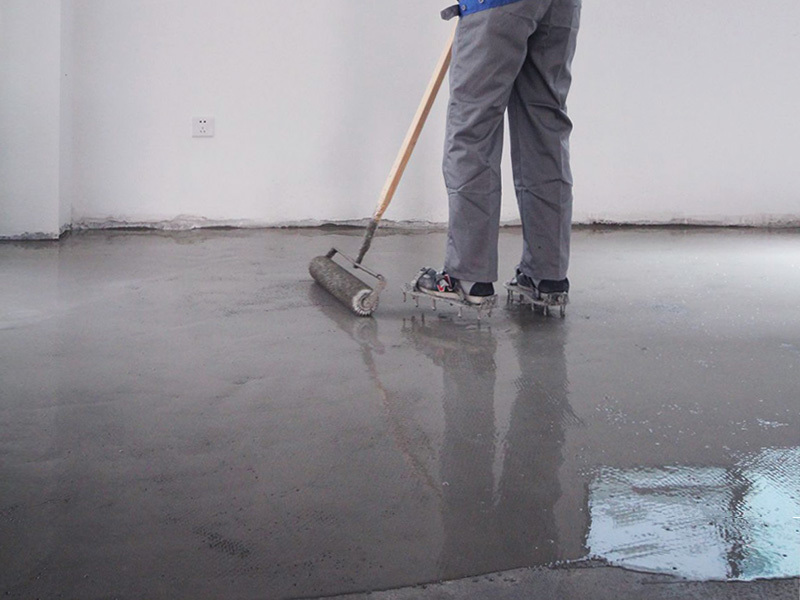
Laying
-
Pour the mixed self-leveling cement slurry on the construction floor, and it will flow and level the base course. If the design thickness is ≥ 4mm, it needs to be scraped slightly with the help of the corresponding rack scraper.
-
The construction personnel then put on special spiked shoes, enter the construction ground, and use the special self-leveling air release roller to gently roll on the self-leveling surface to release the air generated during mixing to avoid the pitted surface caused by bubbles and the height difference of the interface.
-
The construction site shall be closed immediately after the construction is completed. No walking is allowed within 6 hours, no heavy object impact is allowed within 12 hours, and the rubber floor can be considered to be paved after 24 hours.
-
In winter construction, the floor glue board shall be laid within 48 hours after the completion of self-leveling construction.
If the self-leveling needs to be polished, it should be 12 hours after the completion of construction.